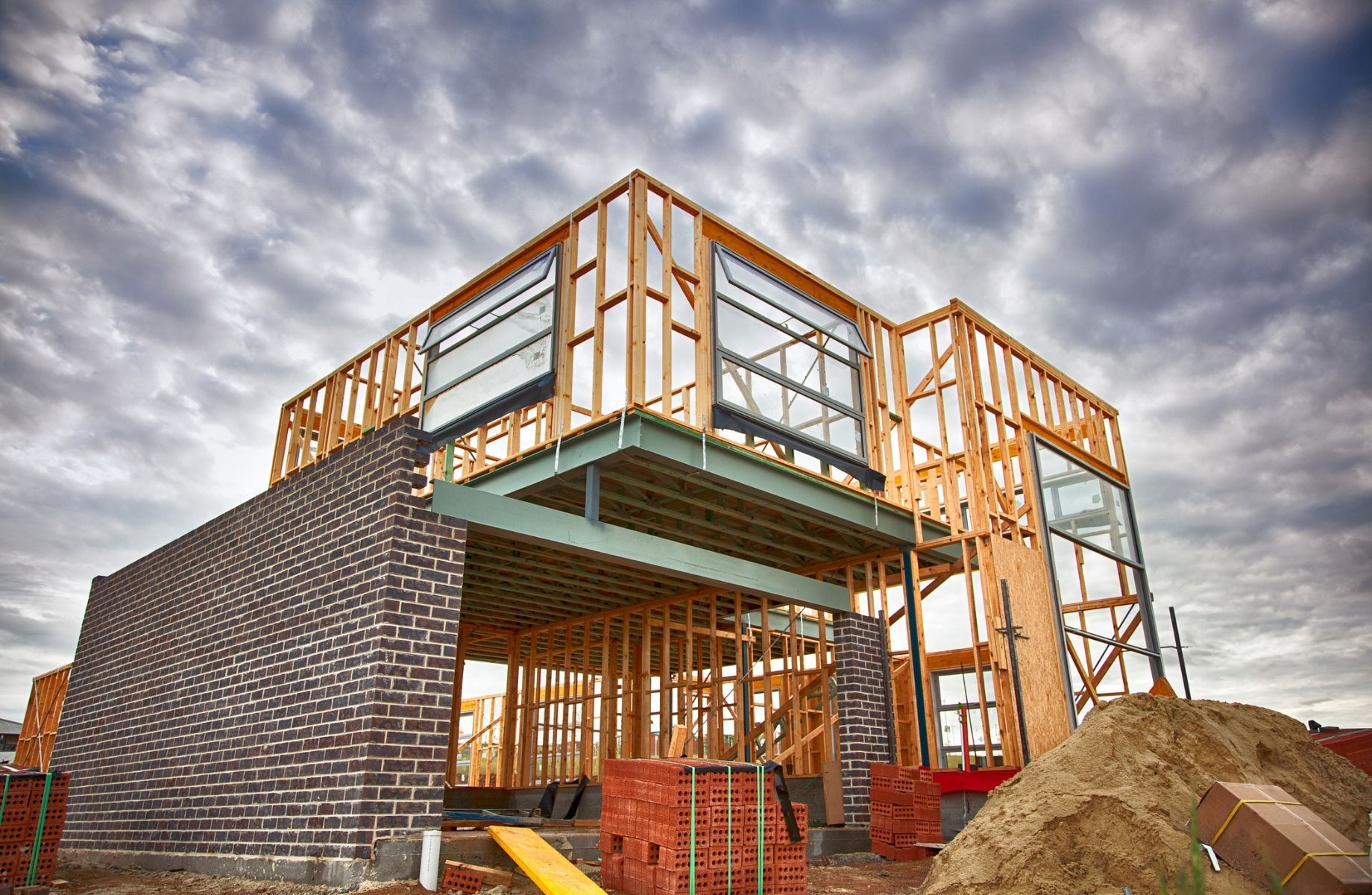
Langcake said while the supply chain issues had not been as chronic in Australia as in the US, new dwelling constructions had significantly affected inflation in the September quarter.
“While global shipping costs remain extraordinarily high, they appear to have plateaued and are broadly expected to recede from here,” Langcake said.
“Nevertheless, we expect it will take until the second half of 2022 before disruptions are fully worked through.”
Hansen Yuncken construction manager Scott Brumfield said the Australian-owned construction group had felt the full brunt of a booming residential housing market and deepening inflation, and called for government support of the locally produced steel industry.
“Delays in sourcing materials from international suppliers especially is not a new issue for Australia, given its geographical location, but [it was] exacerbated by Covid-19 among other factors and we now have a crisis on our hands,” Brumfield said.
“Steel prices have risen by 15 per cent, which is a significant increase when you’re talking about large scale, multi-million-dollar projects, with lead times taking up to 18 months.
Brumfield said steel price increases had bitten into overall costs of projects including the Adelaide SkyCity casino, which used 2200 tonnes of steel, and the Her Majesty’s Theatre redevelopment, which used 950 tonnes of steel. He said planning was crucial in mitigating cost creep.
“The main tactics used to mitigate the crisis is by incorporating shop drawings, or design intent plans, as early as possible to try to give clients an idea of costings and timings to the best of our ability,” he said.
“It is almost inevitable this will be an ongoing issue so addressing it now will actually benefit the industry, and therefore Australia’s economy, long term.”
“Australia’s best insurance is providing support for local capacity of steel production which the federal and state governments have been doing well to promote—more efforts toward supporting local producers would certainly help.”