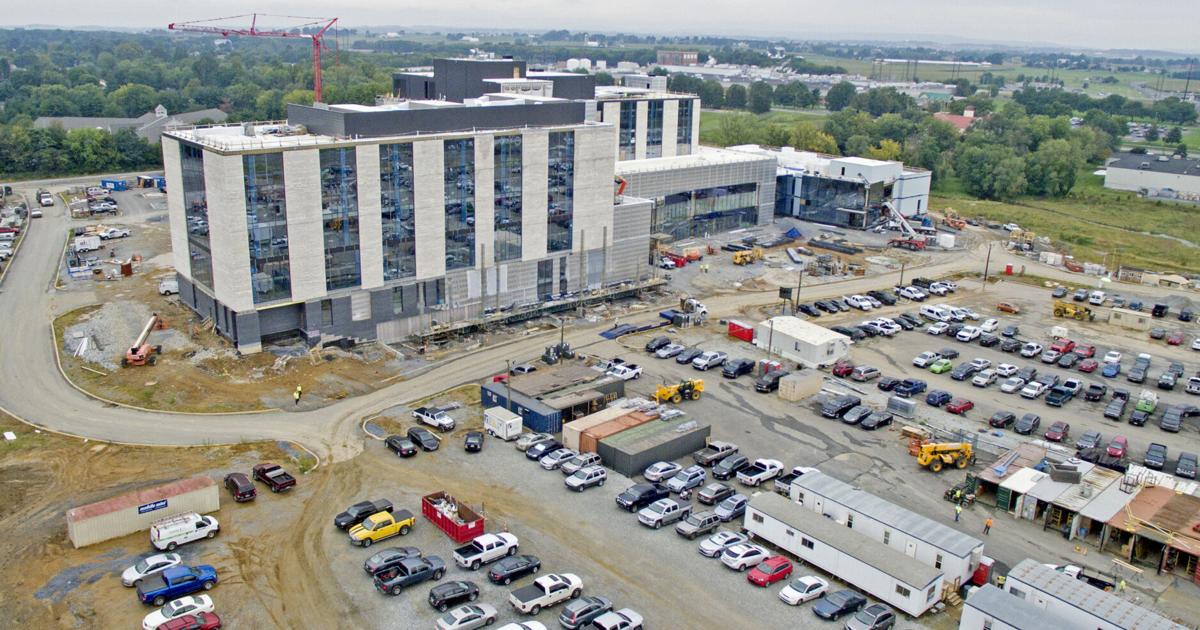
At the ABC Keystone’s annual economic breakfast last month, economist Anirban Basu told hundreds of Lancaster County building industry professionals that 2022 was going to be a year for growth.
Basu, of the Baltimore-based Sage Policy Group Inc., noted construction of multifamily housing, warehousing and manufacturing is and will continue to be strong in central Pennsylvania. Health care facilities and senior housing are also strong, Basu said.
Basu said construction of hotels, malls and office buildings will be weak, due at least in part to changes wrought by the pandemic.
But the war in Ukraine has dimmed that forecast somewhat.
“The Russian invasion of Ukraine will not help,” said Basu in a March 1 analysis. “Oil and other key input prices are rising, placing further upward pressure on the cost of delivering construction services. Those elevated costs have already been leading some project owners to postpone projects in the hope of procuring more favorable bids in the future. Steel, copper, aluminum, neon and nickel prices are all implicated by the outbreak of war, and sanctions on Russia and limits on its exports will be in place long after hostilities end.”
A look at the numbers
National nonresidential construction spending was up 1.3% in January, according to an Associated Builders and Contractors March 1 analysis of U.S. Census Bureau data. On a seasonally adjusted annualized basis, nonresidential spending totaled $838.9 billion for the month.
Spending was up on a monthly basis in nine of the 16 nonresidential subcategories. Private nonresidential spending increased by 1.8%, while public nonresidential construction spending rose 0.5% in January over the previous month.
“Normally, one would look at headline numbers indicating that construction investment rose in America as a reason to cheer,” said Basu in releasing the new analysis. “But the construction spending data are not adjusted for inflation, and in real terms, construction spending was likely down for the month. Total construction spending is up more than 8% from last year, but materials prices are up approximately 24% over that span. Worker compensation costs have also been rising rapidly. As a result, contractor profit margin expectations have worsened in recent months, according to ABC’s Construction Confidence Index.
“Circumstances are worse in the nonresidential construction segment,” said Basu. “While construction spending is up 13% in the industry’s residential component, nonresidential spending is up less than 4% year-over-year. In certain categories, spending is down in both real and nominal terms.”
According to Basu, the fading of pandemic-related construction spending has produced a decline of 35% in the public safety segment year-over- year. Financial impacts on the education sector stemming from the pandemic have resulted in a 7% decline in education-related construction spending year over year. Spending in the beleaguered lodging segment is down nearly 25% without taking into account inflation.
Reasons for optimism
Still the mood is positive among many construction firms.
The Momentum Index, which measures nonresidential building projects in planning nationally, increased 4% in February over January. The increase was a rebound from three consecutive monthly declines that followed a 14-year high in October 2021.
Much of February’s gain was due to a sizable jump in the institutional component, as more education and health care projects entered planning, according to Dodge Construction Network, which calculates the index.
The Philadelphia Federal Reserve’s March 2 beige book said homebuilders reported steady contract signings and construction activity but continued to cite problems securing materials and labor, as well as rising costs for both.
The Fed report, which is based on research prior to the war in Ukraine, said construction activity and leasing activity held steady for most segments of nonresidential real estate. It cited multifamily housing, institutional projects, and industrial/warehouse space as the strongest markets. Prospects for office space and downtown retail will become clearer once workers return to offices on a consistent basis, the Fed said.
Strategies for success
As inflation surges and salaries increase, though, the question remains: How can construction be profitable in 2022?
“How does one satisfy customers and preserve margins when the cost side of the equation is increasing so rapidly?” Basu asked in an interview. “It comes down to operational excellence. It comes to getting the particulars right. What does one need to do in pricing a project? These are really difficult things to do, which is why I do what I do.”
Basu said in the surveys he’s conducted the construction industry is generally upbeat despite the challenges. There’s been some consolidation in the industry.
“This will be a year of growth,” Basu said in his presentation. “But the economy will remain unbalanced, with supply struggling to keep up with demand. Along with rising wages amidst the Great Resignation, that translates into higher than average economywide inflation in 2022.”
Basu forecast even before the Ukraine war that interest rates will increase.
“Beware of rapid declines in commodity and asset prices at some point in ‘22,” he said at the economic outlook breakfast.
Firms with bigger balance sheets and more established banking relationships have an advantage in this atmosphere.
“Generally, it is a challenging time,” said Michael Funck, senior vice president of Lancaster city-based Wohlsen Construction. “We feel really positive about the market and we’ve got a good backlog (of projects.)”
One trick to profitability, he said, is getting materials at better prices by ordering early and even before they are needed.
“For us and for the construction industry, (that means) working to lock in and get our materials as quickly as possible when we are given the go ahead for a project.”
Funck said Wohlsen has created a database tracking materials in order to project lead times to receiving materials and factoring that into project management and bids.
For example, he said, electric switchgear panels are taking up to a year to receive where they used to take about 20 weeks to have in hand. It also means ordering some raw materials, such as two-by-fours, just to have on hand.