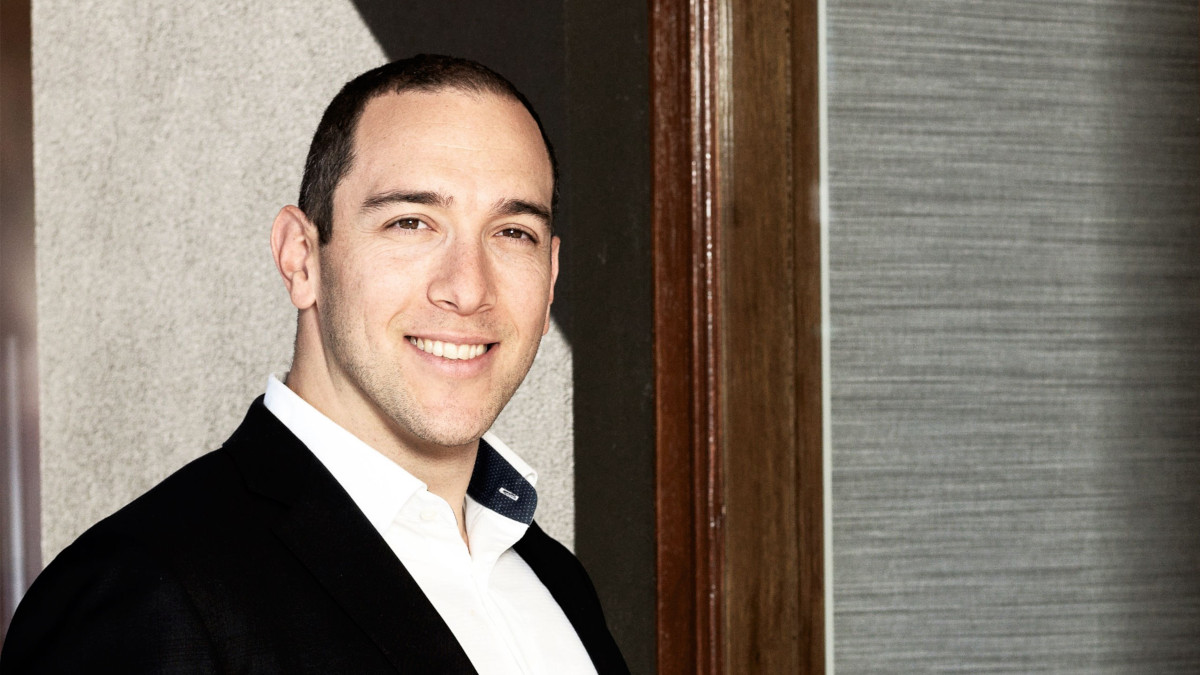
Get set for a big shakeup of the building and construction industry thanks to materials shortages for timber and more, a leading industry figure warns.
According to Max Shifman, the chief of Intrapac Property and national president of the Urban Development Institute of Australia, the mood in the building and construction industry is souring.
The fallout from the Russian crisis and local and global economic challenges are creating tensions that he says will be the new normal for the next few years.
In an interview with The Fifth Estate this week, Shifman says supplies of LVL, structural timber, and soft timber were “definitely a concern” for the development and construction industries.
“Anything that happens here is going to blow out timeframes. We’re already struggling to keep up with demand as it is, just because you’ve got so many different supply constraints, and timber is just one of them.
“Not to mention the fact that we’re also suffering from a major skill shortage, so just being able to get subcontractors and tradesmen to site is a challenge at the moment.”
As The Fifth Estate reported earlier this week, imports from Russia and Belarus account for around 40 to 50 per cent of Australia’s supply of some of the key laminated veneered lumber (LVL) and engineered wood products (EWPs) that are vital materials in many building and construction projects.
The products include formwork LVL, which is an essential component of all concrete constructions for multi residential, high-rise, commercial buildings, and some civil works, as well as i-joist beams and timber flooring systems.
This reliance on Russian imports is likely to lead to shortages of key timber products over the coming months, with importers set to hold crisis talks to discuss the issue with the federal government next week.
The looming shortage of key timber products in the Australian market is set to add to the immense pressures already facing a building and construction sector straining under the pressure of skills and supply shortages.
The threat of a major timber shortage is bad enough for the industry but the problem is compounded by existing shortages across a range of building materials, from plasterboard to aluminium.
That’s not to mention the added cost of electricity, gas, and petrol, which are contributing to inflationary pressure across the economy.
“It’s not only timber. There are issues with everything from concrete pipes to plasterboard to steel in some areas. It’s really very concerning, and has been for some time. And it doesn’t appear as though there’s going to be any short term fix for it,” Shifman says.
“We’ve recently seen the price of raw aluminium go up in the order of 40 per cent because of the lack of supplies. That filters through into all sorts of things that you’d need for building materials, aluminium windows for example. It’s quite acute in that space.”
It’s not just about upfront prices – it’s the flow-on costs
A key issue is the fundamental laws of supply and demand: a shortage of timber is likely to flow through to higher upfront prices. But that assumes you can get supplies of those vital building materials to begin with.
“There are some things that, unless you’ve ordered months in advance and paid for months in advance, you just cannot get them. Full stop,” Shifman says
“In a construction program, if you’re missing something along the way, the rest of the program gets blown out. And so you might have seen reports of house building times, pushing out dramatically and that’s going to continue.”
While the construction sector is close to capacity, Shifman says delays caused by skills and supply shortage means the amount of actual work being completed on a monthly basis is dropping.
“You can’t get those efficient construction programs to line up anymore because, at any given point, you’re either missing a piece of material or you’re missing the labour to install it, and it’s dragging everything out. And that’s going to be a dynamic that continues for the foreseeable future.”
Most building companies are used to fairly manageable supply chains and they tend to lock in pricing for an extended period of time which means they’ve got some certainty so they can work on low margins.
The trouble is that those margins have been eroded over the past 12 to 18 months, he says.
“There has to be a conversation around working with builders and clients to see if there’s a middle ground that can be struck. Builders are stretched to the point where they just walk away from their businesses, but also that clients appreciate that we’ve just gone through an unprecedented and unexpected period,” Shifman says.
Did the stimulus package cause the issues?
Much of the blame has been placed on the Morrison government’s housing-focused stimulus packages, such as HomeBuilder.
But Shifman says it’s easy to look back and say the stimulus has exacerbated the issue – but few would have predicted the perfect storm of local and global issues that the construction sector is facing.
Those packages were the right thing at the right time, he says.
But what we didn’t anticipate was the level of supply chain crunch that would arise subsequently, because other parts of the world had similar ideas. “We just saw this incredible boom in housing starts globally.”
Long-term consequences for housing affordability
All of this – combined with surging inflation and interest rates – means the pipeline for new project starts is likely to slow dramatically, with a spillover impact on house prices.
There’ll be higher risk and less certainty preventing the industry from locking in prices, Shifman says.
Added to that is the risk of a vicious cycle. A return to normal migration rates, which we need to have because we’re all struggling with a lack of labour across so many industries, is likely to push up house prices. At the same time, a lot of projects won’t be viable because of the higher costs.
“That’s going to be the new normal for a while.”